▼日本のFAはどうなっているの?
インダストリー4.0と騒がれてから随分経ちましたが、最近はあまり聞きませんね。シーメンス社(ドイツ)が工場のFA化をリードしていると言われていましたが、現在はどうなんでしょうか?
今回のフェアーの入り口で、オムロン社製の協調ロボを展示していた山崎電機株式会社さんとお話させていただきましたが、現在のPLC( programmable logic controller :工作機械をコントロールする機械)には、ほとんどLANのくち(Ethernet端子)が付いており、シーメンス社が推奨していたインターフェースが無くても情報を取得することが可能であるとの事実を知らされました。
そういった意味では、特別な通信環境を別途設けずとも、機器の稼働状況をオンラインで監視したり、制御したりできることになります。
▼メーカーごとに違うPLCの規格を乗り越えるには
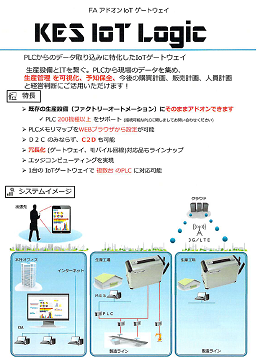
FAについて全くの素人なので、記述内容に誤りがあるかもしれませんが、普通のIT的理解で記述させていただきます。
工作機械から出力される情報を得るには、様々な方法があります。例えば、3連ランプ(稼働・停止・異常をランプの色で示す)の点灯状況を光センサーで取得してサーバーに送る方式や、そもそもそのランプのメーカーが出している点灯状況をWiFiで送る装置を使用したりして、実際の機械の状況を得るのではなく、アナログ化された情報(ランプの点灯状況)をIOTに使用するパターンと、株式会社金沢エンジニアリングシステムズさんのように、PLCが出力する情報を直接取得する方法があるようです。
IOTに求めるものにより、コストパフォーマンスに合った方法を選択できるのは良いことだと感じています。
▼目的は「労働生産性向上」

色々とセミナーに参加して、先進的な取り組みを行っている会社さんの例から、一番苦労されているのは、「作業の進捗をどのように取得するか」であると思いました。
ある企業では、タブレット端末を置いて、業務の開始と終了をボタンを押すという方法で簡素化していましたし、今回のフェアーでは北陸コンピュータサービス株式会社さんが「サイコロを使って作業状況を記録する」方法が案内されていました。
これはとても良い方法だと感じました。
パソコンやタブレットは、使用環境に制限があります。暑かったり、寒かったり、水が掛かったり、ほこりが舞っていたり。でも、給電を考える必要があるかもしれませんが、サイコロみたいな物体に、どの面が上かを判断できるセンサー(ジャイロセンサー)で作業状況をシステムにアップできれば、作業者の負担は大幅に削減できるとおもいました。生産性向上は、いかに現場の方に負荷をかけずに、状況を情報化するかが鍵だからです。
▼FRIDの技術的なブレークスルー
業務効率化で絶対必要なのは、「物の存在の確認」です。在るものを確認するのは、人間の仕事として今でも残っています。なぜでしょうか。物を認識するには、認識するための方法が必要ですが、今ある技術、例えば「バーコード」「QRコード」「OCR」など光学的な処理で情報を取得する必要があり、重なり合った商品をカウントすることはできません。
この難題を解決してくれるのが、「FRID(Radio Frequency Identification)」。電波でタグ情報を読み取る技術なのですが、周りに金属があると読めないらしいです。(理屈は理解していません)

もし、金属で視界が妨げられていても、一発でFRIDを読むことができたら、製品や材料の棚卸が劇的に合理化されるでしょう。そんな夢みたいな技術をもっているのが、株式会社フェニックスソリューションさんです。
適正在庫が企業経営の基礎である事は、重々承知していますが、生産活動に忙しくて、在庫調査をこまめに実施することができないのが現状だと思います。
導入コストとの兼ね合いは当然あると思いますが、棚卸の人件費と在庫削減効果を足した経済性と導入コストを検討するに値すると思います。
また、FRIDは、工程管理にも役立つソリューションだと考えています。トヨタの看板方式ではありませんが、製品にFIIDタグを付けてラインに流し、製品の到着と次工程への移送をトレーシングすると同時に、到着時に、どのような加工をすべきかなどの情報をディスプレイに表示させることも可能になります。
非接触だから大体の場所にあれば読み取れます。作業者にもFRIDの付いた社員証を持たせれば、いちいちリーダーに読ませる必要がなく、単に、作業場所に居るだけで認識される利点があります。何をするかも、あらかじめ用意した作業名を書いたFRID付きのプレートをリーダーにセットするだけ。正確な作業時間の記録が、オペレータの負担を低くして得られると考えられます。
従来よりFRIDの有効性について着目していましたが、電波が通らないものには向かないという特性がありましたが、電波の回り込みを制御できるのであれば、工場の製品や資材などの管理につかえるなと感じました。FRIDの広がりを感じさせてくれました。
▼即戦力化に強力な仕組みを
働き方改革は、生産性の向上であると言ってきました。今2人で行っていた作業が、1人でできるようになったら、残りの方は何をすべきでしょうか。という問題が必ず発生します。
つまり、仕事は誰が行っても、間違いなく、同一品質で行える環境が大切です。

業務のマニュアル化も大切ですが、作業自体を機会がアシストして、間違えにくい環境を整備することも重要です。そんな社会的要求の中で、一つのソリューションとして「キティイングナビ」という仕組みを株式会社富士通ITプロダクツさんが提案していました。
ピッキング業務は、単調な作業である事から、思い違いによる選択ミス、個数ミスが出がちです。
同社のノウハウと、開発済みの部品を駆使して、廉価にキッティングのサポートシステムを構築できるそうです。
人財の有効活用と品質向上には、機械によるサポートは不可欠であろうと考えます。まだ実装はされていないようですが、棚に重量計をセットして、個数間違えも感知するのも良いと思いました。棚卸も自動化できるので、ぜひ製品のラインナップに追加してもらえればと感じました。
重さを作業の正確性のチェックに加えると、発送前の最終確認にも役立つと思います。人間の目と総重量をチェックすればかなりの精度になるのではないでしょうか。
▼見える化は一番の近道
セミナーで聞くお話で、「匠の技」がよく話題になっています。何か問題が発生したら、「匠の技」で原因のあたりをつけて、まずやってみる。経験がなせる技です。
しかし、工程が複雑化すると同時に、人間が感じることができる「差」によるトラブルより、もっと制度が要求されています。やはり今「何が起きたか」を知ることが解決の近道でしょう。

そんな要求にこたえてくれるソリューションを株式会社日西技研さんが提案していました。
AIの分野では、音声と画像の分析は、人間を超えたともいわれています。超高速カメラとAIの掛け合わせで、どんな製品ができるのか、「開発中」の文字に期待が高まります。
▼製造・物流もIOTやAIの活用はこれから
様々なサービスやデバイスが生まれてきていますが、これらを業務で利活用することが、企業成長の要と言っても過言ではないでしょう。少子高齢化が叫ばれて久しいですが、これからが実経済に影響が出てくるでしょうが、「人手不足は、天の恵み」と捉えて、業務改革、生産性向上を先頭を切って断行してゆかねばなりません。
Comments